
Many new coolants have been developed to meet the needs of new materials, new cutting tools, and new tool coatings.
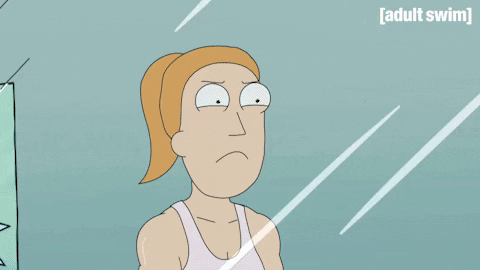
There is a wide variety of cutting fluids available today. The chip load value is normally provided by the tool supplier, such as the sample below:įor example, to calculate the feed rate for a 5/8” end mill cutter with 4 flutes from the table above, you'd use the following formula:įR = 10.24 inches per minute (ipm) Choosing Your Cutting Fluid (Coolant)
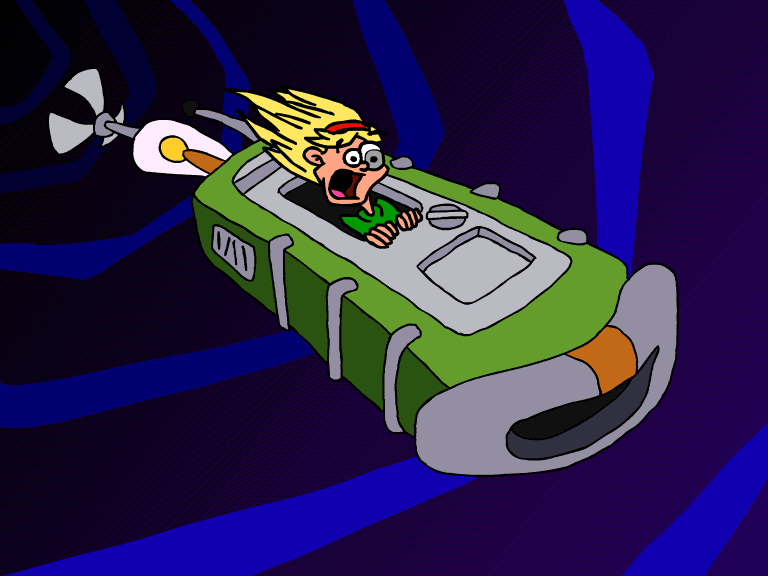
The chip load is the radial depth of cut the cutting tool makes in one revolution. Chip load, also referred to as feed per tooth, is a term used to describe the thickness of material removed by one tooth on the tool's cutting edge.
FINE TUNE GIF MACHINE FREE
Request our FREE white paper here<< Calculating Feed RatesĪnother important aspect to remember when implementing any CNC strategy is the feed rate. > Learn everything you need to know about the metal machining process. Here are some standard SFPM you can use when working out the RPM for common metals:įor example, if you wanted to calculate the RPM of a 5/8” (0.625”) end mill cutting mild steel: The simple calculation to work out the Rotations Per Minute (RPM) of the cutting tool is: the outside diameter, of the tool in feet per minute. Having a cutting speed that is too high can incur extra costs as the cutting edge deteriorates quickly, but conversely, a low speed can reduce productivity and production rates.Ĭutting speeds is calculated in Surface Feet Per Minute (SFPM) is a unit of velocity that describes how fast the cutting edge of the cutting tool travels, or in other words, it’s the speed at which the material moves past the cutting edge, i.e. When using CNC machines, cutting speeds are important to understand as they can determine the efficiency your production can achieve. Here we look at speeds and feeds rates for milling. You will need to use different formulas for the different types of tools used within the CNC machine. By utilizing a materials database and knowing the detailed specification for each CNC machine, the ideal feeds and speeds rates can be calculated. The best practice for establishing the optimal rates for the material is to use a feeds & speeds calculator. First, you need to identify the goals you want to achieve, which can include:
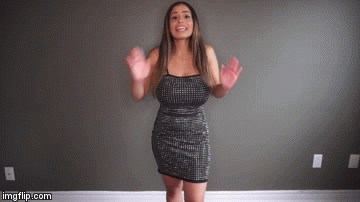
To get the best possible results from a CNC machine, you need to cover a lot of ground. Traditionally, the starting point for this would be either a machining data handbook or the experience of senior machinists on the floor. One of the major challenges a CNC programmer faces every day is identifying critical metal machining parameters such as depth of cut, spindle speed, and feed rate. Does your production process include Computer Numerical Control (CNC) machining of metal parts? If it does, you might have recurring issues with your metal finishing as is common with this process.
